Quality at the Source is one of the most powerful principles of lean management. It is a quality management system based on the ability to monitor quality not only at the end of the process but at every process step.
By establishing the quality at the source system, we change the approach that “the quality team is the keeper of the defects of each process; the processes only increase productivity.” Instead, we empower each process unit to be the keeper of its defects.
We increase the awareness of significant and recurring errors in each process. In addition, we ensure that the team improves frequent and essential errors with methods such as Kaizen and 8D.
We develop team leaders to spend a significant portion of their time trying to prevent variability affecting quality.
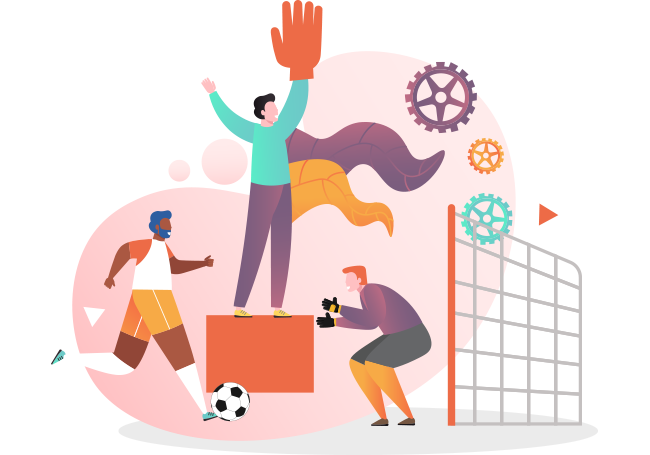
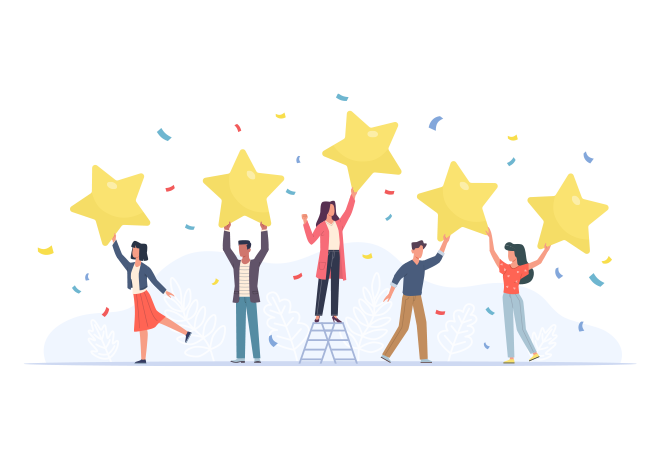
While management prioritizes quality at every opportunity, employees recognize that quality comes before quantity.
Increased process control, triggered by customer complaints and errors detected at the final inspection, leads to increased productivity.
By teaching and practicing techniques such as Poke Yoke and Jidoka, we help develop solutions to prevent errors from occurring.
Suggestion systems ensure that the team prevents errors before they grow.
The five components of Quality at the Source:
- Standard Work
- Auto-control
- Successive controls
- Visual management
- Processes designed to prevent errors and Continuous Improvement
Through our training, implementation, and development activities, we establish the five components of Quality at the Source and ensure that each operator becomes “his/her controller.”
Each employee becomes well aware of the importance of the product or service for customers and customer expectations.
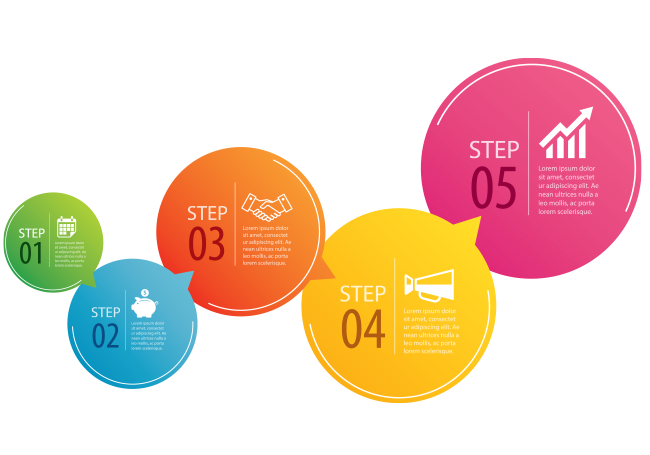