Giving importance to continuous improvement is not only one of the values of Lean Management but also one of the two pillars on which all lean improvement tools are built.
Stiza changes how your teams look at problems and problem-solving by creating a culture of continuous improvement in your company.
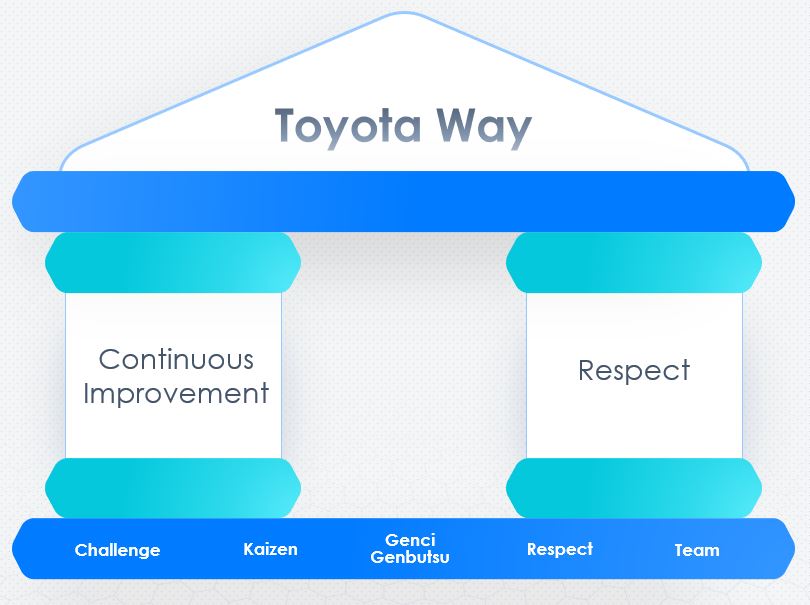
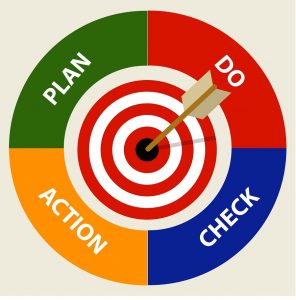
With Stiza’s teamwork, teams internalize the importance of planning and the impact of preparation and analysis on the solution.
Employees develop the practice of analyzing and questioning the root causes through activities we call Before/After Kaizen or Rapid Kaizen and build their competencies for improvement activities that depend on multiple factors, which we call Major Kaizen or Kobetsu Kaizen.
It is as essential to adopt and spread the habit of solving some problems with the kaizen tool during reviews as it is to develop the ability to use kaizen well as a tool.
Stiza helps team members gain practice and competence on which problems to solve with OPL (one-point-lesson) and which problems to solve with kaizens during Asakai reviews.
As the Quality at the Source approach becomes established, the expectation of permanent solutions to quality problems increases, and the team uses 8Ds and kaizens more widely.
As the teams review the OEE results, they quickly come to a consensus on which kaizens to apply to the machines and lines with the lowest availability and which kaizens to apply to the points with the highest performance loss.
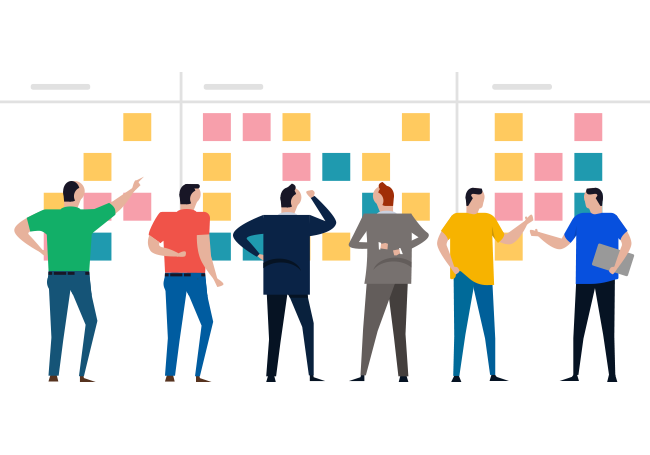
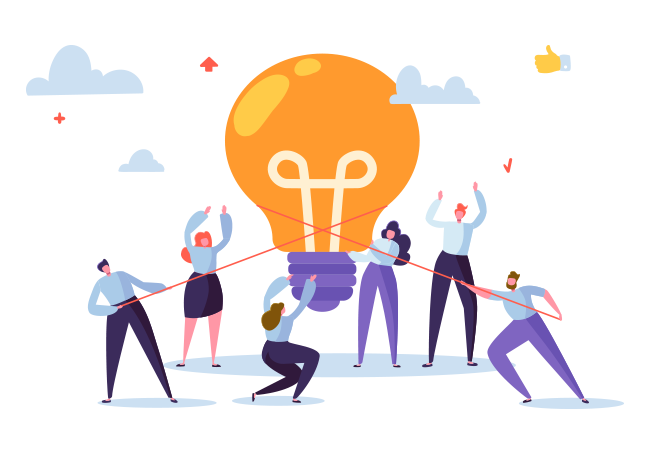
With the widespread implementation of a suggestion system, employees give suggestions about problems in their environment without waiting for a review and solve relatively complex problems with the help of kaizens.
Stiza’s practice of loss hunting or muda hunting helps teams make the problems taken for granted visible and resolve them through the suggestion system and kaizens.