Asakai is a meeting that takes place as early as 8:00 or 9:00 in the morning, where the organization’s managers gather in front of a board with relevant indicators and do a quick status review on safety, quality, losses, productivity, etc.
It is a very valuable ritual and habit of the lean approach. Yesterday’s accounting is done quickly and opportunities for improvement are discussed. It improves communication and accountability. In large organizations, Asakai meetings of smaller groups take place before the management-level review. Usually, in front of the group SQDCM board, each team leader shares the situation with the other team leader of the relevant unit.
The meeting starts with whether there were any safety issues from the previous day. While not hearing about a work accident is expected, not hearing about a near miss after a week or more can be interpreted as underestimating the risks.
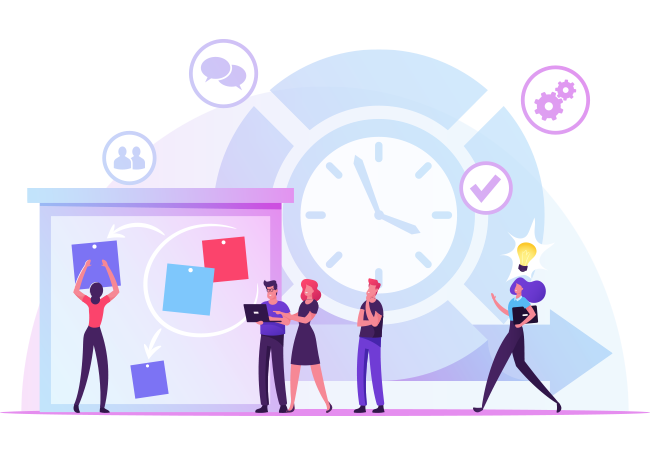
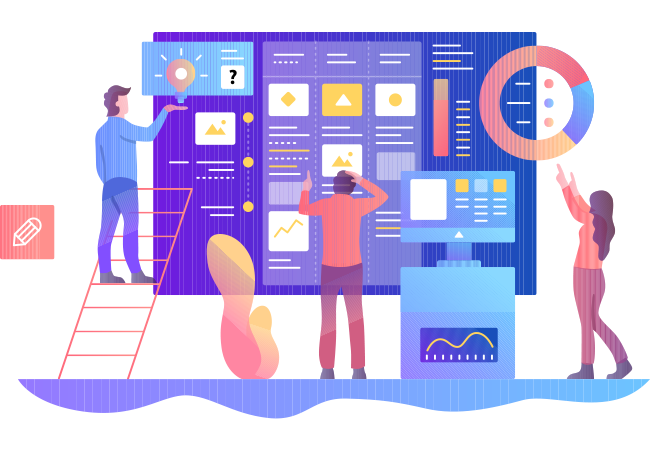
Leaders do not find explanations such as warning the operator as an action appropriate. Instead, they expect to hear that they have organized an OPL (One Point Lesson). Unfortunately, the OPL alone is often not enough and it is common to plan a temporary self-control activity.
If the problem is more complex or recurring, the relevant leader takes responsibility for taking action by analyzing it in depth with kaizen.
Kaizen may not be required for actions to be taken quickly. However, even without kaizen, it is helpful to include the problem and solution proposal in the suggestion system to understand better the variations in case the problem recurs.
After the quality topic, leaders also discuss plan compliance, OEE, production efficiency outputs, and employee motivation and development.
Asakai reviews are expected to take place quickly in order to be sustainable. In a plant that is trying to establish the Asakai habit for the first time, it may be recommended to start the reviews with a single topic that they consider most important, for example quality issues, and add other matters in the following weeks.
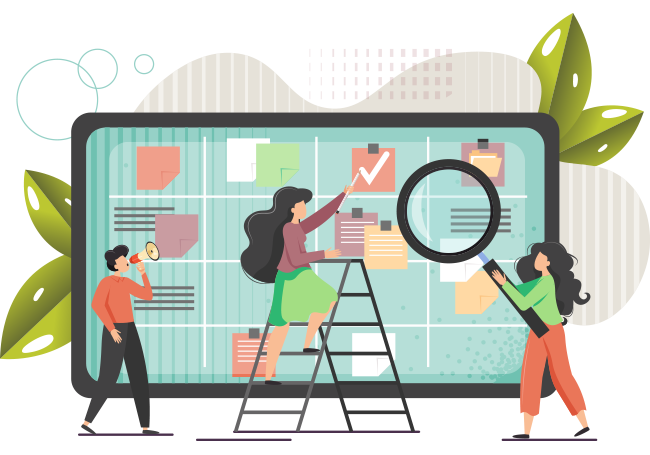
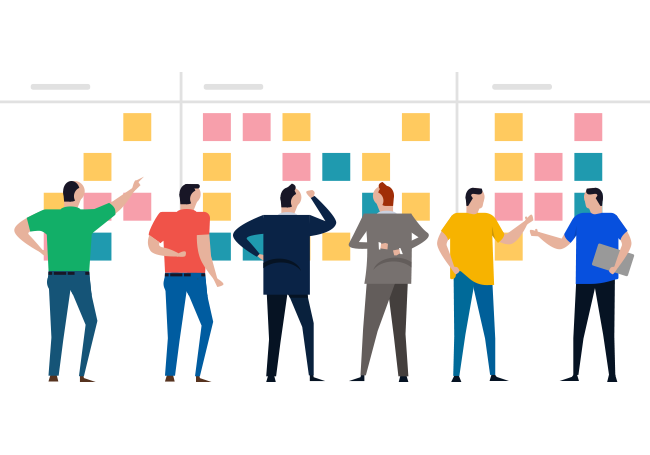
In reviews, leaders not only account for the previous day but also discuss the variables of the current day. The team reviews what measures have been taken to deal with any variables, such as the lack of an operator, who will replace them, how well-trained they are, what different material or method they will be using.
Stiza ensures that this small but very important habit is embedded in your organization as a culture. It ensures that the reviews go far beyond “talking the talk”.