SMED, which stands for Single Minute Exchange of Dies, is a lean management tool used in manufacturing to reduce equipment changeover time. SMED aims to save equipment downtime by completing as many of the steps required by the changeover as possible while the equipment is running and quickly transitioning to process the following product.
The traditional choice to reduce the operational change burden of a product change in production has often been to try to produce products together, even those needed a few days or weeks later because they are similar.
Toyota argued that accumulative production was the wrong strategy and reduced die-changing time from the longest operational changeover of about 3 hours in the 1940s to 1 hour in the 1950s.
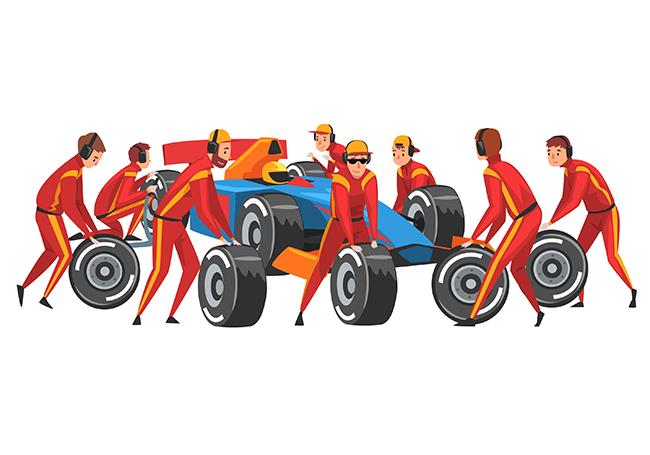
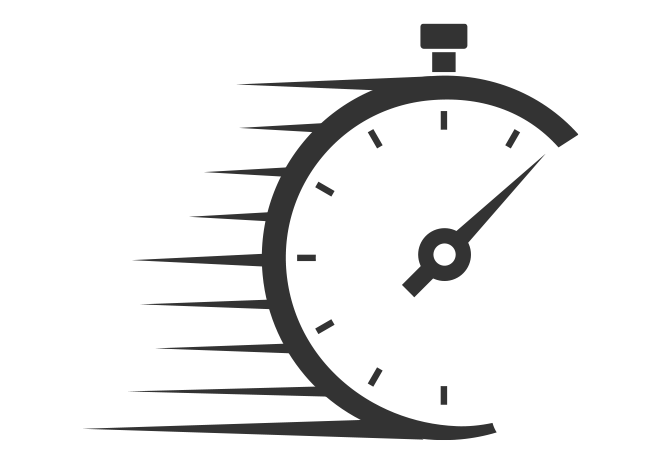
Operation changeover time may not approach single-digit minutes with a short period of effort. For example, for the Japanese automotive industry, it took 20 years to get close to the 10-minute limit and 30 years to experience 3 minutes. Today, companies are in a position to improve operation changeover in a much shorter time by utilizing many tools developed around lean principles.
Developments such as the widespread use of external set-ups, preparation process improvements, tools, apparatus standardization, etc., offer excellent opportunities to improve operation changeover times.
Through video analysis and on-site observations, Stiza helps your team gain experience in improving changeover times and helps to extend this technique to different machines and lines.
Contrary to popular belief, the primary expectation in the SMED effort is not to reduce the total time consumed for operational turnaround losses.
Companies that reduce turnaround time but do not give up the habit of accumulative production cannot reduce their in-production stocks, nor can they take advantage of the opportunity to deliver customer orders with shorter delivery times.
Stiza strives and insists that SMED efforts aim at achieving shorter delivery times. In addition, SMED improves planning performance by facilitating the pull system and flow establishment.
With SMED and pull system improvements, companies increase customer loyalty by realizing shorter delivery times and better performance with delivery plan compliance.
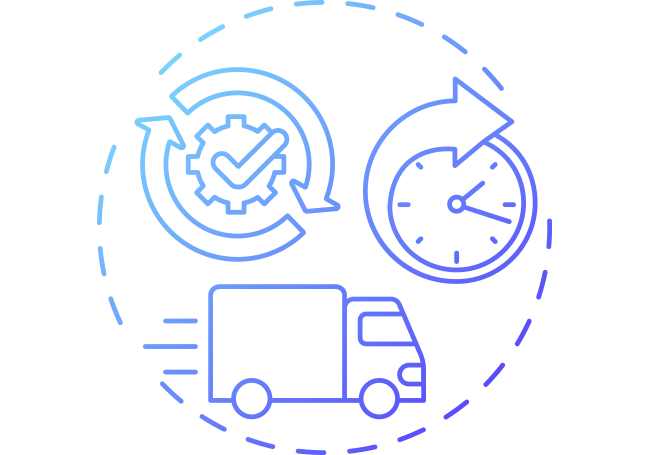