The 8 Disciplines, referred to as 8D for short, is a problem-solving technique. It is usually a means by which a supplier methodically informs its customer that they have correctly identified, taken the corrective action, and analyzed and taken preventive measures for the part or process a problem reported by a customer. Organizations can use 8D as a communication tool to prevent quality defects between their suppliers and customers and, within the organization, between supplier and customer processes.
8D is one of the essential components of the Quality at the Source approach.
Ford first published it in 1987 under the name Team Oriented Problem Solving, and in the late 90s, Ford revamped it as G8D to make it a global standard.
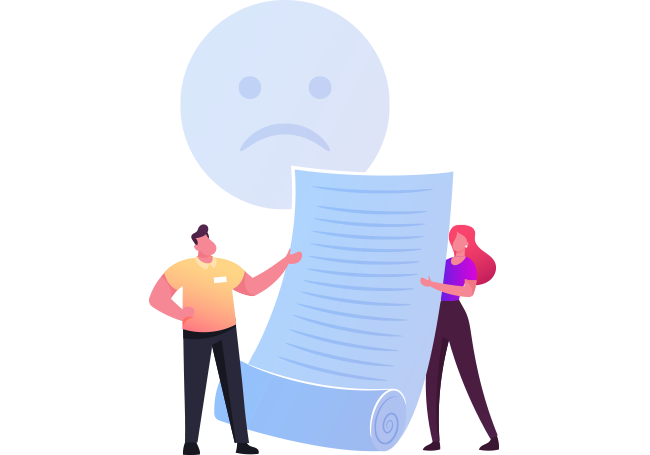
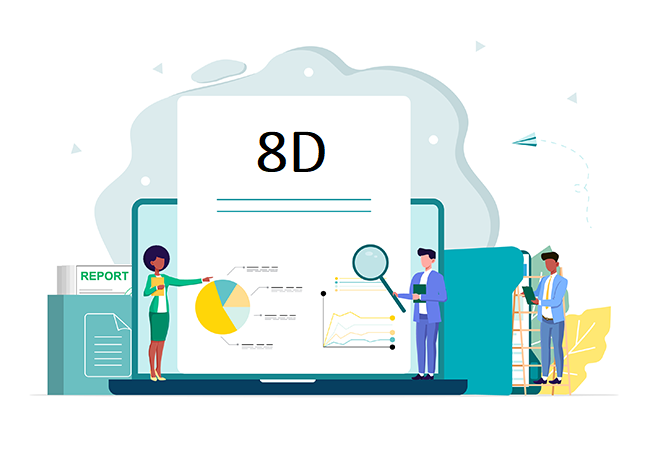
Industries other than automotive widely use 8D because of the following benefits.
- The technic provides a permanent solution as it focuses on the root cause,
- Prevents the recurrence of the problem and similar problems,
- Strengthens the control system by analyzing how the error can escape the control system,
- Improves learning,
- Embraces the inadequacy of fire extinguishing,
- Creates a culture that can solve different problems by developing a team approach,
- Gives confidence to the customer.
D1: Team formation
People who work at the point where the problem occurs and who are familiar with the process form a team that is generally not more than eight people. Team members can agree on the purpose and goal of 8D.
Champion: Provides the necessary resources and leadership for the team’s suggestions and activities. Participates in team meetings to review and support decisions. Responsible for the 8D.
Team Leader: The business manager and spokesperson for the 8D team. She forms the group, defines roles, and leads the team towards goals and tasks per the 8D methodology. Works in coordination with the champion. She maintains neutrality in discussions, organizes 8D meetings, and shares meeting notes without a rapporteur.
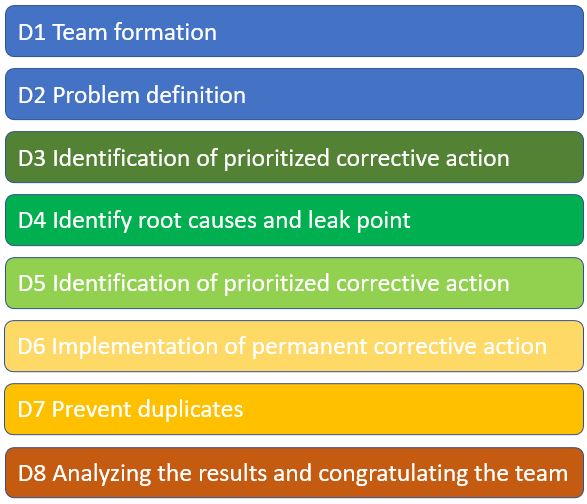
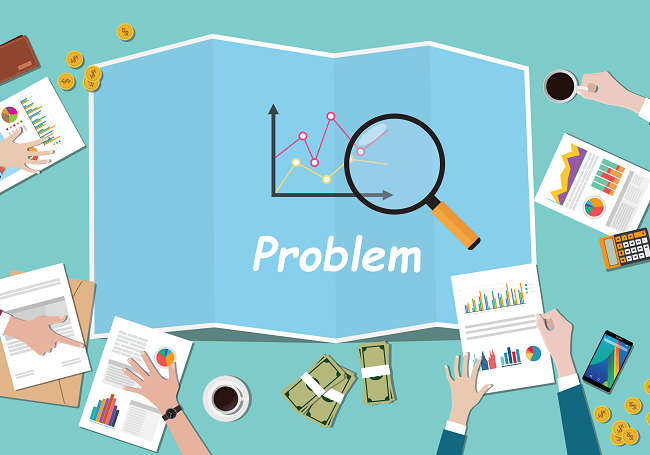
D2: Problem definition
The team creates a short but clear and specific definition of the problem. While defining the problem team finds answers to the questions like:
- Where and when the problem occurred
- What was affected, what caused problems
In this step, in addition to a short and specific definition, it is good to provide additional documents to show that the team well analyzed the problem and handled it correctly.
Analyses such as 5W1H, which shows the variables that may affect the problem, or the Pareto diagram or process flow, where the influencing factors are listed, can be accessed through these documents.
D3: Identification of prioritized corrective action
In this step, the team takes action to show that the problem is under immediate control.
For example, if there is stock, the team explains the total number of products and semi-finished products blocked, the kind of sorting process done, actions to avoid the same error in the ongoing production, and additional controls made.
In addition, if the supplier delivers products after these controls, the team informs that they have used a different label indicating they are good parts.
If the defectively separated products are to be repaired, how the repair will not cause a new defect is also among the expected explanations.
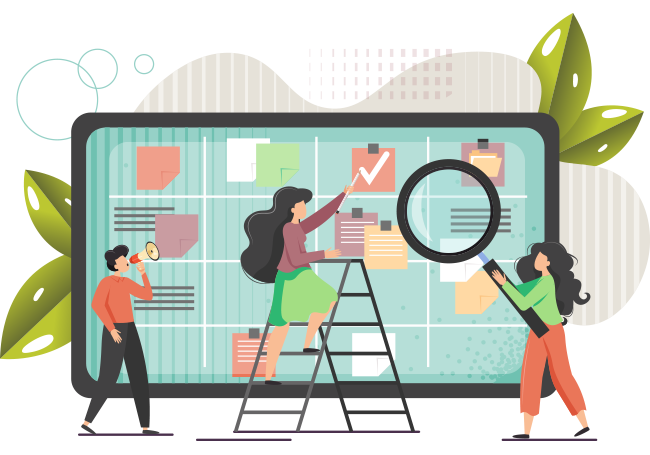
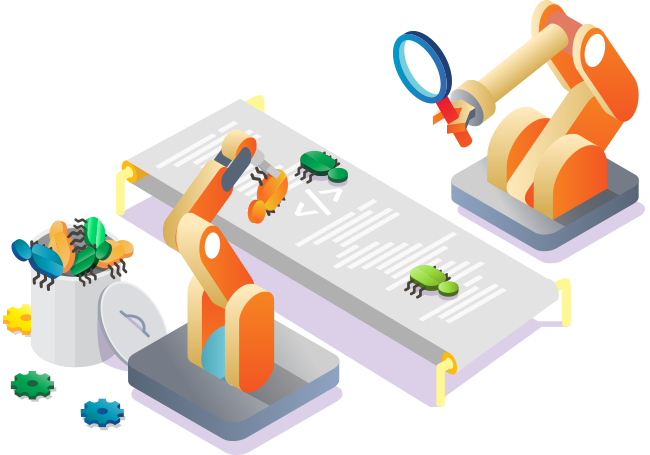
The group makes a fishbone analysis to ensure that they have sufficiently evaluated potential causes listed during the problem identification phase. This analysis helps us remember some of the factors we may have missed. Next, we must validate all the potential causes we have listed before reflecting on the root causes. Validation is an essential step. Not only does it prevent us from mistakenly presenting a non-valid probable cause as a good cause, but the observations and analysis made during validation positively impact root cause quality.
Root cause analysis directs us to the source of the factors by asking why five times for each good cause. Sometimes a reason may have more than one root cause, or multiple causes may have a single common root cause.
Root cause analysis helps us with both preventive and corrective actions.
D5: Identification of prioritized corrective action
It may take a long time to take action on the root cause; however, it is also not desirable to maintain the operation process subject to 8D with a high level of attention and control. Therefore, the team must take quick action for the process steps affected by the root cause. In the root cause analysis, one or more of the reasons between the root causes and the apparent causes are candidates for a more effective corrective action. By taking quick action on a step between the root cause and the apparent cause, the team brings the level of quality and control back to normal.
D6: Implementation of permanent corrective action
While action to the root cause enables operators to pay little attention and effort to maintain the process control, an act to the apparent reason makes operators spend a lot of attention and effort to retain the control process. Therefore, even if the team cannot take immediate action on root causes, they implement the prioritized action.
Once the team implements the prioritized action, which they believe to be permanent, verifying the results and observing the stability is essential. At this stage, the team needs to be aware that they haven’t yet taken any action against the root cause. Therefore, it is necessary to follow the progress of the 8Ds with lists and tables so that temporary improvement does not become permanent comfort. The table includes the planned schedule for the 8D steps, the actual schedule, and a brief description of the following step action.
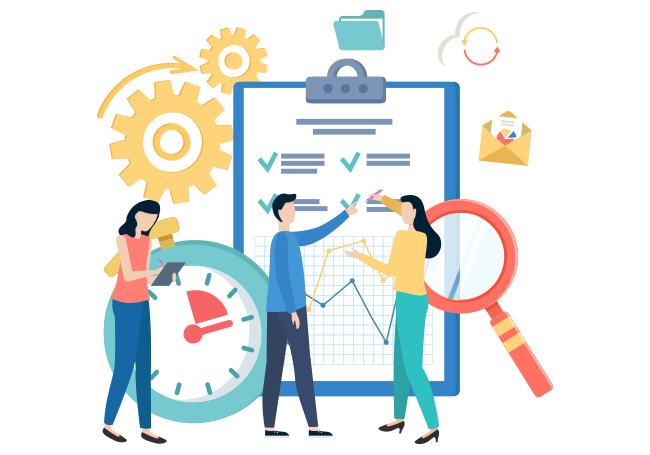
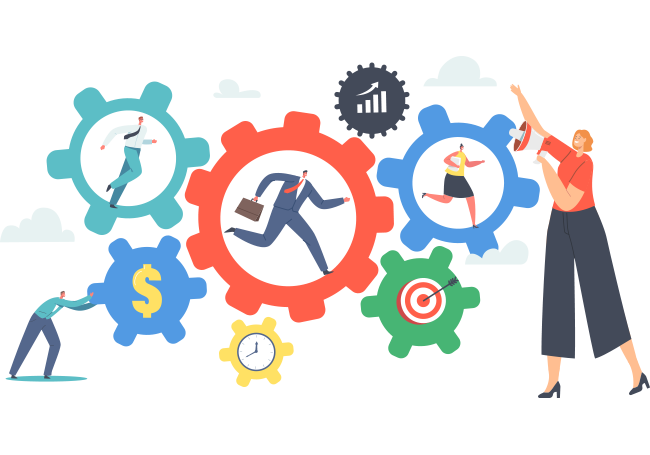
D7: Prevent duplicates
Step 7 requires action on the root cause as planned to prevent the error from happening again. The fact that the team has taken the root cause action and the results are good does not yet mean that 8D has achieved its purpose.
In step 4, we again question the adequacy of the action on the root cause of the error that the team identified during the root cause analysis.
The team also scrutinizes process steps that could not prevent the root cause from occurring. They make process improvements to prevent similar errors from happening again with queries such as whether the company performed had an FMEA process that could prevent the root cause from occurring or if they accomplished whether there were any missed points. The team documents all of these opportunities in lessons learned form.
D8: Analyzing the results and congratulating the team
In the closing part of 8D, the group shares the completed activities with brief notes on how they verified the results. It is helpful to fill in a simple completion checklist to ensure nothing is missing.
When the management agrees that 8D can be closed, they congratulate team members on their analysis and actions.
Stiza ensures the effective use of 8D in your organization, which is one of the cornerstones of a sound customer complaint management system. In addition, supporting you to excel in on-site quality practices brings you forward in the competition.
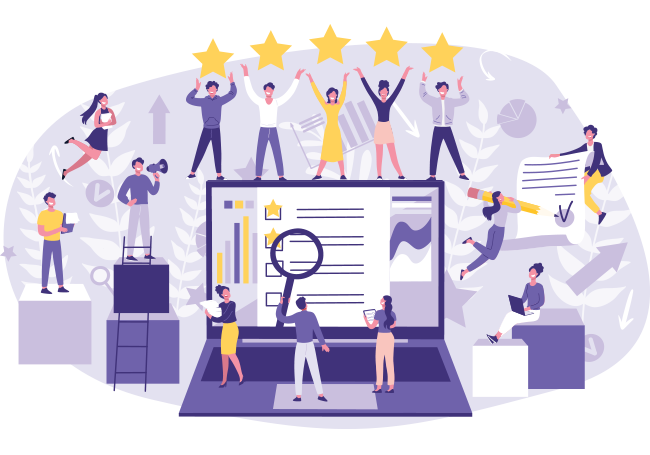